One of the latest industrial applications on blockboard, consists in overlaying the panel with a durable decorative surface material, called continuous high pressure laminate (cHPL or CPL). This panel has special performance properties including chemical, fire, and wear resistance, which add to the well-known great features of blockboard.
Some of the most common enforcements are structures for upper and lower kitchen cabinets, workbenches, child room and office furniture, and all kinds of articles that require excellent resistance to scratch and hard use.… Read more...
Engineered parquet and floorings
Wooden floors are nothing new, but parquet floors have seen a recent resurgence as more people are starting to introduce these elegant and sophisticated styles in newly built homes or whilst renovating old properties. The patterns are timeless and classic, and always look chic.
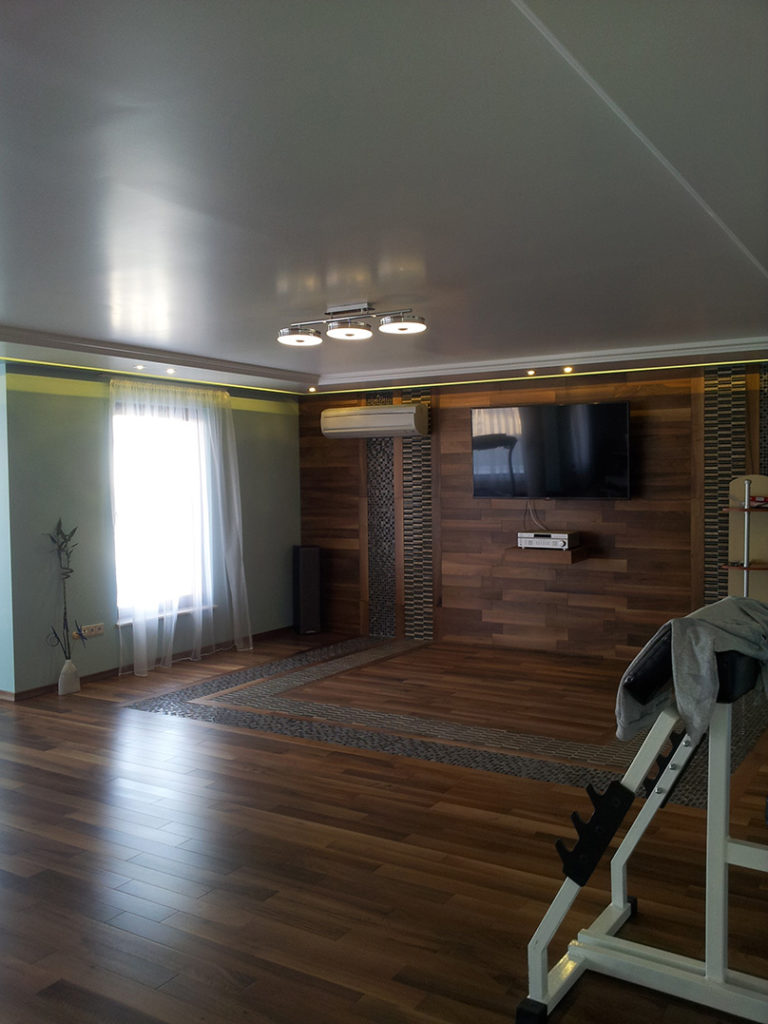
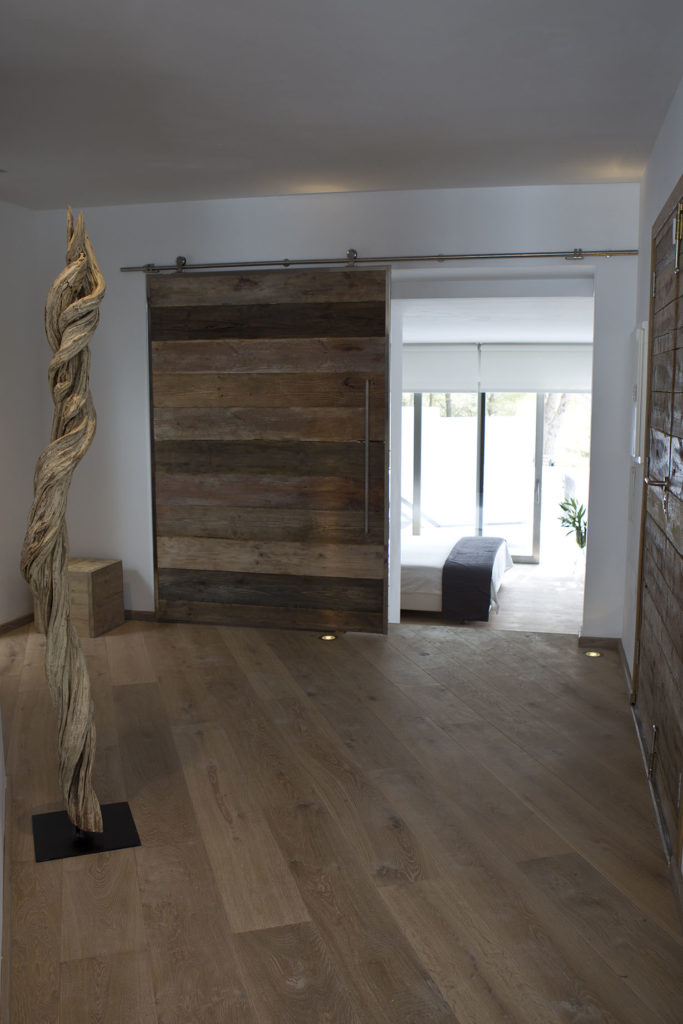
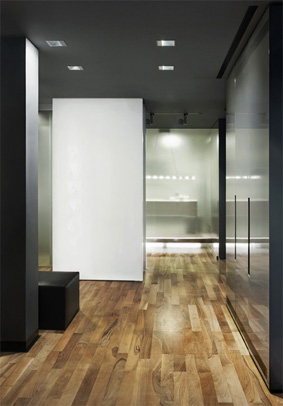
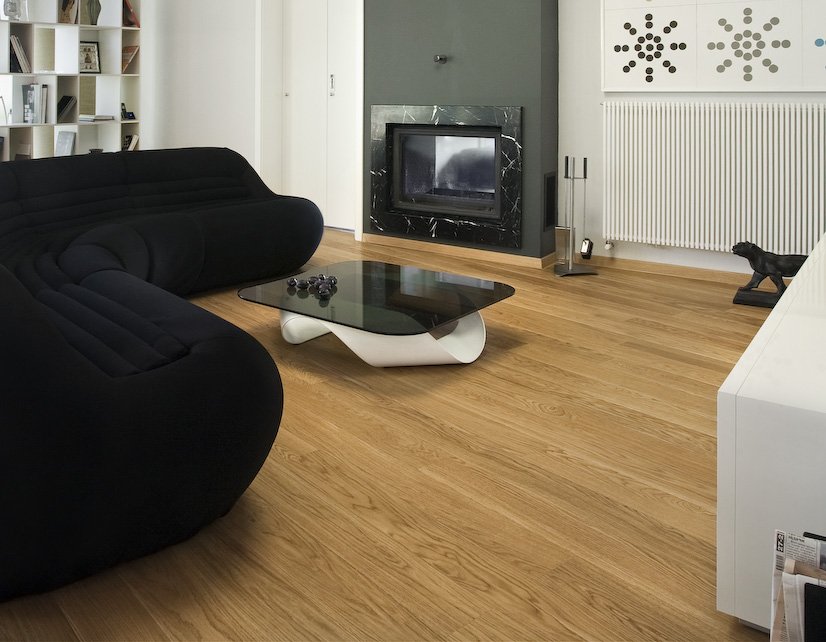
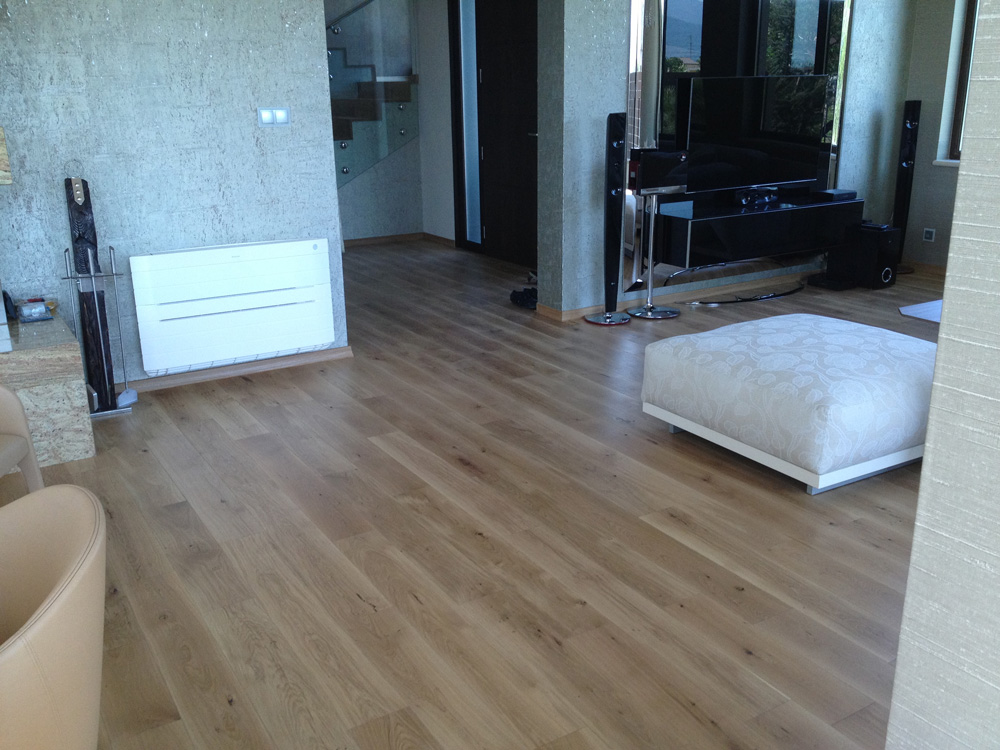
The word parquet comes from the French ‘parchet’ (short for ‘parc’, literally meaning “a small enclosed space”).… Read more...
Double-core blockboard, the thick lumber core
Double-core blockboard is a special kind of construction to produce thick lumber core panels, generally in the thicknesses between 34 mm and 60 mm.
This kind of panel has superior bending strength, lightness and screw-hold ability in comparison to any other kind of wood-based panel.
While the most common application is door frames, it’s suitable for the production of high-quality door, tables, and structural furniture components like shoulders.… Read more...
Block-board, the solid lumber core panel
Block-board (also called lumber core) is a timber material consisting of a core of wooden strips placed between two layers of veneers (3-ply in all), with extraordinary characteristics of bending strength, lightness and screw-hold ability. As it’s a real solid-wood alternative to timber, suitable for the production of high-quality and long-lasting furniture, furnishings, partition walls and cabinet-making.… Read more...
5-layer blockboard, the light and stable lumber core
Blockboard (aka lumber core) is well known worldwide due to its characteristics of bending strength, lightness and screw-hold ability. As it’s a real solid-wood alternative to timber, suitable for the production of high-quality and long-lasting furniture and furnishings. It is commonly used for shutters (also with large dimensions), structural components (shoulders), long book shelves, partition walls and cabinet-making.… Read more...